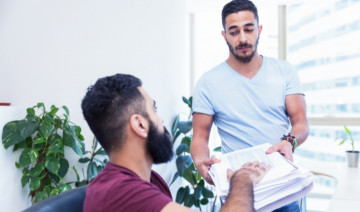
Coping with an Enormous Backlog
In the current market, getting jobs is not the problem; moving them into, and through, production is the challenge. Here is one solution.
When there is a surge in leads, sales and projects in design, remodeling companies are left with the challenge of getting projects through pre-production (estimating, design, material ordering and project planning) quickly and accurately to get jobs into production. Business owners that are facing this challenge can look to improvement of their pre-production processes.
There are many ways to approach process improvement. "Lean" is a method of process improvement that works particularly well in the remodeling industry. It is an approach borne out of the Toyota Production Company some 70 years ago that has evolved into a great tool for all types of business.
1. Map "Current State"
Lean process improvement begins with mapping the “current state.” Mapping is a step-by-step visual of each step in the process, how long each step takes and which team member handles that step. The current state is the way we are doing things now, not how we should be doing them, how we are actually doing them.
2. Identify Waste (including Time Wasted)
Once the current state is mapped, teams get together to look at the process to identify waste. In our industry, two of the most common forms of waste are waiting and defects. Waiting generally occurs between steps – waiting for the estimate to be done, waiting for the customer’s selections to be made, waiting for the boss’s approval. The time it takes to actually complete a step like actual design time, time working with the client on selections or reviewing the work with the boss is usually small compared to the time spent waiting between steps.
Defects are another common form of waste in our processes. Defects are anything that is not done completely or correctly the first time and requires time to undo, correct or rework. Defects are often the result of poor communication or poorly defined processes. They become even more frequent when there are demands to get work done quickly and when people are working on different types of projects for the first time.
3. Brainstorm "Future State"
The next step in lean process improvement after the current state is mapped and the wastes are identified is to brainstorm the “future state.” The easiest way to do this is to look at those steps in the process that have waste and ask the questions “in a perfect world, how would this step be done to avoid waiting or defects?” In answering that question we start to determine what the obstacle is to a better process.
4. Identify Possible Improvements
The teams then identify a list of possible improvements that could be made that would reduce or eliminate the waste at each step. Each idea is considered for how much of an improvement it would create and how easy it would be to implement.
5. Management Decides Which Improvement to Implement and Measure
Management then decides which ideas to put into practice and then measures their results.
Lean is a relatively simple process:
1. Map "Current State" >
2. Identify Waste (including Time Wasted) >
3. Brainstorm "Future State" >
4. Identify Possible Improvements >
5. Management Decides Which Improvement to Implement
... but not an easy one. It requires the discipline of going through the steps one-by-one and focusing very much on those things that are part of our processes that take time and effort but don’t add value to the customer. It also requires a recognition that the best ideas for process improvement come the people that are actually doing the work. They know best what slows them down, creates frustration or gets in the way of a smooth process.
So, how does this method relate to our pre-production processes and the need to get work into production quickly and accurately? Let’s look at one example.
Doug’s Remodeling Company (fictional) is a design-build firm that does high-end kitchen and bath remodeling and home additions. Once a design agreement is signed, the company takes about 16 weeks to get projects into production. The pre-production process includes: meeting with customer, learning about their desires for the project, getting bids from subcontractors, preparing the estimate, preparing a scope of work, getting customer selections, doing final designs, ordering materials, scheduling the project, getting permits and various other tasks along the way. In each one of these areas, we have identified the time it takes to actually do the work for that phase, time spent waiting between steps in that phase and time spent fixing or reworking particular steps. After the team maps the current state, identifies wastes, considers the ideal state and then brainstorms solutions, they come up with ideas like: checklists for certain steps, limiting options for selections, better training on design software, internal deadlines for ordering materials earlier and a format for more detailed scope of work. This would be a different list for each company, but this is what our team identified. By implementing these ideas, improving communication and finding other things to improve along the way, our pre-production process drops from 16 weeks to 12.5 weeks on average, and our quality improves.
The benefit is that we have list time (and therefore less cost) tied up in the process. Projects move more quickly toward a production start date. Customers are less frustrated with a long process, and less demand is put on our team to get the job done. It is a win-win in every sense. And now with pre-production moving better, we can take the same approach to our sales process, production process or other aspects of the business. Eliminating waste becomes part of our culture and our every day routine. And our business becomes easier to manage, more competitive and more profitable.